case studies
Case Studies
Hudson has developed a specialized knowledge base from being heavily involved in many dry cargo trades. From this experience, Hudson has developed innovative methods that allow Hudson to implement its GOLD© Standard, decreasing customers' costs. Learn more about some of the techniques that Hudson has practiced and perfected by clicking on the Case Studies below.
DRY POWDER CARGO HANDLING
HOLD CLEANING ARRANGEMENTS
STREAMLINED STEEL SERVICES
ADVANCED LUMBER STOWAGE
MARINE-FRIENDLY HULL CLEANING
COMPLETE MINERALS TRANSPORT
CROSS-CONTINENTAL TRUCKING
WEATHER SENSITIVE DISCHARGING
LINKING REMOTE SUPPLY CHAINS
Dry Powder Cargo Handling
Hudson has developed a specialized knowledge base from being heavily involved in many dry powder cargo trades. As a result, Hudson ensures that the loading and discharging of dry powder cargoes can be accomplished as quickly as possible. A critical component of this effort is the use of specialized machinery to assist in dry powder handling operations.
Hudson is exceptionally skilled at moving dry powder cargoes, an aptitude that Hudson has honed over years of extensive involvement in the industry. The efficient loading and unloading of such cargoes can be a daunting task. However, Hudson overcomes such challenges through the use of innovative techniques and specialized equipment.
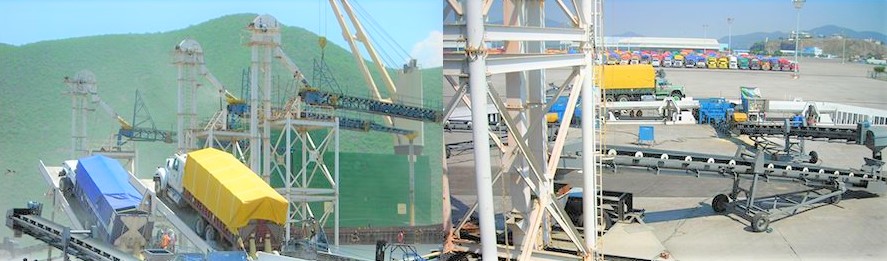
Ordinarily, grabbed cranes are used to handle dry powder cargo; this process is wasteful and slow, especially for large vessels. In order to swiftly, safely, and economically load dry powder cargo Hudson turns to traveling retractable loaders, high-capacity conveyors, and electric hydraulic rotating ship loaders with choke feeders and dust control technologies. For unloading, Hudson employs vacuvators, which ensure rapid unloading with minimal spillage.
These specialized pieces of equipment allow Hudson to load up to 1,500MT of dry powder an hour, while at discharge Hudson is capable of unloading 1,000MT an hour. Hudson works closely with its common ports of call to ensure high-capacity loaders and vacuvators are available to handle its dry powder cargoes. Where a port does not have discharge vacuvator facilities, Hudson deploys mobile vacuvators to ensure the safe and economical unloading of cargo.
The vessel’s discharge port is often not the final destination for the cargo. Where overland transit is necessary, Hudson employs road or rail assets to convey the cargo to its final destination. Should a parcel require narrow waterway transit, Hudson deploys vacuvators to lighten the cargo from the vessel into waiting barges. Hudson then uses bulldozers and other heavy equipment to trim the loaded cargo, allowing hatch covers to be fitted and spillover waste to be reduced. Tugs then push the barges to their final destination. By using these inventive methods, Hudson ensures quick vessel turnaround and maximum hold utilization, which translates into flexible schedules and lower costs for Hudson's customers.
Hold Cleaning Arrangements
Hudson’s vessels carry many different types of cargoes during the course of their voyages. While it is preferable to always carry “clean” cargoes, it is not uncommon for a cargo to leave the holds filthy and in desperate need of cleaning, as is the case in the photograph below.
When cargoes leave a residue, like the petcoke cargo in the photograph on the left, it is imperative that the holds are swiftly and thoroughly cleaned and prepared for the next commodity. Hudson has therefore developed comprehensive guides and proprietary methods to ensure the vessel's holds are readied effectively for sensitive commodities, irrespective of what cargoes were carried previously.
The picture to the right is the same hold after a complete Hudson cleaning regimen. Typical onboard cleaning supplies and methods are simply inadequate to attain such a high level of cleanliness. Hudson ensures that all of its vessels, transfer equipment and terminals have access to the required chemicals and tools necessary to produce immaculate holds.
By cleaning holds quickly and efficiently, Hudson's fleet is always ready for most dry bulk commodities. Hudson's customers, in turn, benefit with adaptable and streamlined supply chains, ready to face the logistics challenges of a truly global economy.
Streamlined Steel Services
Hudson has been managing steel supply chains for over 50 years and has developed an efficient and streamlined procedure for quickly and safely handling steel in line with Hudson’s COST© principles.
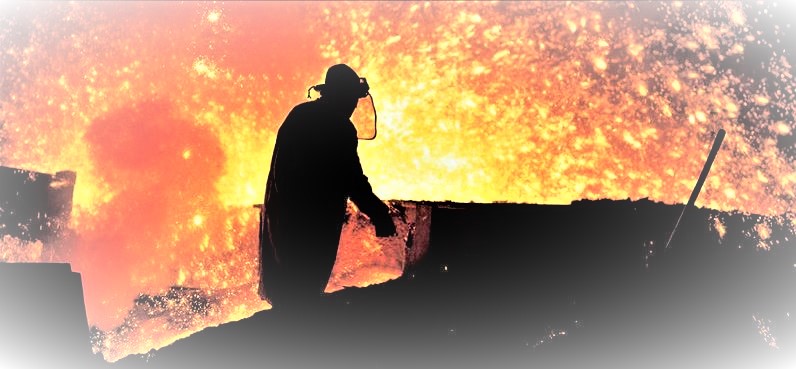
The following is an overview of how Hudson puts its experience to work handling the process of shipping steel products including some techniques and equipment utilized.
Hudson is very particular about the procedures used to stow its customers’ material. High quality WPM certified wooden dunnage is used between gear loads to protect the material and prevent it from shifting during transit. Hudson uses only WPM certified dunnage guaranteed to be heat and methyl bromide treated, bark-free wood that is free of pests. Proper stowage ensures the material is stable, secure, and protected during what could be a long voyage with many port calls along the way.
Steel bars are lashed together with signode tape (a form of steel strip engineered for a higher break strength at a thinner gauge and lower in cost than normal steels trapping) and loaded onto the vessel. Hudson does not simply secure steel with some wire and turn buckles and then instruct the ship master to tighten everything enroute after it inevitably becomes loose. Hudson takes great care in using the proper equipment to make sure the job is done correctly the first time, avoiding any unnecessary surprises or extra work during or after transit.
A custom designed spreader bar is used by stevedores to increase discharge speed. Spreader bars are used to evenly distribute the weight of bulky materials across a wider surface. This increased stability allows more cargo to be carried with each gear load, leading to a faster working rate. Hudson makes extensive use of spreader bars and other specialized equipment to ensure faster and safer loading and discharging of its cargoes, a key part of achieving COST©.
- Steel is color coded at the producing mill at each end to identify its grade.
- As the material departs for the loading port, Hudson SCM personnel label and barcode each piece of steel individually, keeping careful track of the parcel to ensure its integrity. Hudson takes every precaution to prevent missing material.
- Following a pre-approved stowage plan, the material is organized to be block stowed by customer and grade for quick and orderly loading onto the vessel. Hudson implements COST© principals to achieve effective loading speed as soon as the vessel arrives.
- The material is loaded onboard following the stowage plan, where it is stowed, lashed, secured, and dunnaged according to Hudson’s exacting standards.
- Hudson's personnel are on hand to monitor and expedite the loading while overseeing each step of the process.
When a piece of steel is labeled and barcoded, it is entered into our inventory control system. From here Hudson can monitor the status of each individual piece of steel in transit from the mill until it is delivered to the customer’s door. Integration of the latest technological advances is critical in achieving cost effective supply chain management.
In the photo to the right, shore gear is used to unload a gearless ship. In accordance with COST© principles, Hudson strives for flexibility and has access to equipment to utilize either a ship’s gear or shore cranes. When efficiency dictates, shore cranes are used to supplement ship gear or to replace damaged or slow gear to increase load or discharge speeds. Hudson at times will also discharge straight into barges to accommodate clients with those requirements using the principles of COST©.
As steel arrives at the designated storage area, it is cataloged to ensure the parcel integrity is maintained at the destination. In a similar process to the loading arrangements onto ships, steel is also organized by grade and load for fast loading onto trucks and rail for delivery to customers. As per COST©, Hudson understands that time is money, and does its best to ensure that no time is wasted. Hudson believes that careful planning will reap dividends, and it is with this understanding that Hudson has developed the procedures and obtained the equipment necessary to ensure a smooth, safe, and efficient steel supply chain.
Advanced Lumber Stowage
Stowing lumber with this new type of lashing increases the amount loaded. With the use of creative load techniques, careful planning, and cooperation amongst all partners involved, Hudson was able to increase the total amount of lumber loaded on board by 18%.
When a forestry customer approached Hudson to transport its products across the Atlantic, Hudson recognized an opportunity to create value for the customer by employing its PEARL© management system. Hudson’s expert operations and voyage planning departments collaborated with its shore captain and stevedores in order to develop a comprehensive stowage system for the customer’s lumber parcels. The result was a method which utilized innovative loading techniques to maximize vessel capacity while minimizing costs.
Through the use of this innovative method, careful planning, and cooperation between all parties involved, Hudson was able to load 18% more lumber per voyage than the customer’s in-house logistics department. The realized increase in vessel capacity resulted in immediate and significant savings for the customer.
Hudson secured these efficiencies through the inventive use of pallets and lashing, which Hudson produced to assist in the loading and discharging of the lumber. This investment in new lashing allowed for more accurate loading while also creating a safer work environment for stevedores and staff. At discharge, the new lashings allowed for the quick attachment of crane wires and hooks which allowed Hudson to minimize personnel and vessel costs.
As exemplified by the above, the adaptive application of cutting edge resources is a key element of Hudson’s PEARL© management system. Through the innovative use of new materials and techniques, Hudson maximizes vessel carrying capacity while reducing total loading time, leading to flexible schedules and increased profits for its customers.
Marine-Friendly Hull Cleaning
Hudson utilizes ecologically safe cleaning techniques to increase efficiency and minimize its impact on the environment.
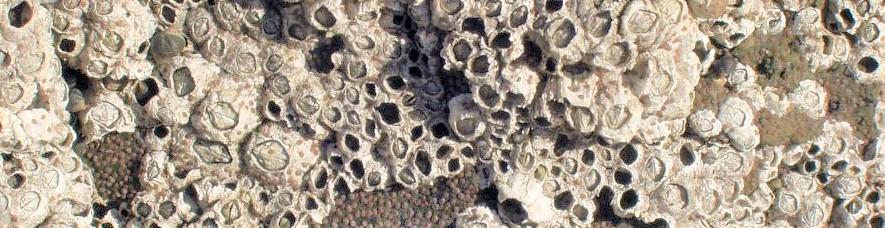
During the course of its voyages around the world, a Hudson vessel will encounter a wide variety of marine life. Unfortunately, some of this marine life wants to hitch a ride. “Fouling” is the process of plant and animal life growing on and attaching itself to underwater structures such as ships, oil rigs, and other ocean platforms.
When a vessel experiences fouling, also known as biofouling or hull fouling, marine plants and animals begin to fasten to the vessel’s hull, propeller, and external areas. Animals such as mussels, barnacles, and other shellfish adhere to the vessel’s surface and begin to reproduce in great numbers. Larger vessels can accumulate up to 90 tons of biofouling.
To combat this problem, Hudson employs both passive and active measures to keep underwater surfaces as clean as possible. Non-toxic anti fouling paint is used to deter organisms from latching onto the vessel. When prudent, Hudson hires dive teams to clean the hull using light buffing equipment and other suitable tools. Near ideal conditions are necessary for divers to be effective, so Hudson is proactive in cleaning the hull when conditions permit instead of waiting for the fouling to become severe. In addition to the ecological and efficiency aspects, failure to keep a vessel’s hull clear of fouling can lead to expensive time in dry dock, which can result in costly delays.
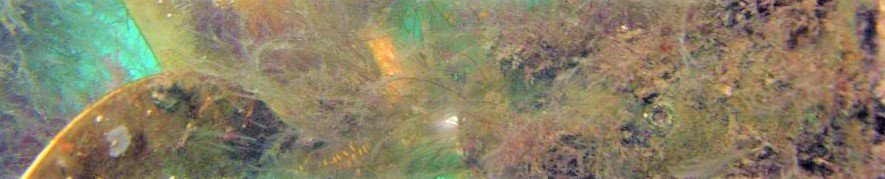
Plant life including algae and seaweed will also spread rapidly along any underwater surface, clogging vents and inhibiting propellers. The difference in efficiency between a clean hull and a fouled hull can be as much as a metric ton of fuel a day and cost a vessel half a knot at the same engine RPM’s. Most importantly, fouling can be ecologically disastrous as it can provide a conduit by which invasive species can travel from port to port.
Through the enforcement of rigorous cleanliness standards, Hudson keeps its vessels clear of fouling and thus maximizes vessel efficiency. These standards save the customer both time and money while keeping emissions low and ecosystems safe.
Complete Minerals Transport
Hudson leverages new technologies and its historic expertise to ensure safe, flexible and efficient mineral transit.
Hudson has specialized in comprehensive mineral transport for over fifty years, creating a mine to mill transit infrastructure which provides for a fast, reliable, and economical mineral supply chain.
Once minerals are excavated from the mine, Hudson uses road and rail resources to transport the minerals to the nearest shore-to-ship transfer facility, often using conveyors or grabs to transfer the minerals onto a Hudson vessel. Hudson safeguards against contamination by supervising the loading process and ensuring the vessel has suitable holds. Grabs are often used, reaching a transfer speed of up to 600 metric tons of minerals per hour per hatch. Where port infrastructure allows, Hudson prefers to use conveyors which can transfer up to 1000 metric tons of minerals per hour per hatch.
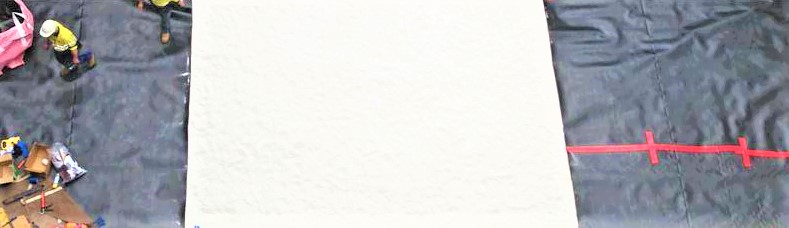
It is not uncommon for a customer to ask for different grades to be loaded for the same voyage. Standard procedure is to load grades by hold. However, Hudson’s proprietary GOLD© Standard techniques allow Hudson to reliably load multiple mineral grades, separated in the same hold, providing its customers with unparalleled flexibility in mineral transport.
At the receiving facility, Hudson utilizes vacuvators to ensure a safe, efficient transfer. Throughout the transit process, Hudson leverages new technologies and its historic expertise to ensure safe, flexible, and efficient mineral transit, allowing its customers to rest easy when they ship with Hudson.
Cross-Continental Trucking
Hudson utilizes road assets to efficiently transport barge covers across the United States.
When asked by a customer to source high quality removable hatch covers for use on barges in Asia, Hudson knew it would take a global effort to execute this ambitious goal. Hudson identified a suitable manufacturer for the 2.5 ton covers in the American South. Hudson then provided on-site feedback to the manufacturer to ensure compliance with specifications and exacting quality standards.
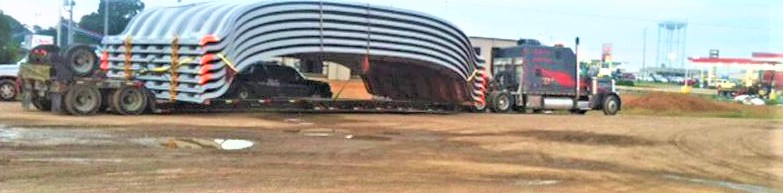
Hudson next applied its PEARL© management system to identify the most efficient way to move the covers to the coast. Hudson examined all available options, including rail, road, and water solutions. Rail transport options were quickly eliminated as the massive size and unwieldly shape of the covers made loading and unloading impractical. Water transit was also eliminated as an option due to the unnecessary cost and complexity which would result from using multiple vessels to transport the covers. Thus, after much evaluation and analysis, road transport was identified as the quickest, safest, and most efficient way to move the covers to the coast.
Barge covers this size are very rarely transported across the United States, much less internationally, and therefore, the project required expert planning to ensure a smooth journey. Physical obstructions, narrow roadways, tunnels and bridges were identified, analyzed, and addressed. Hudson also worked with local agents and authorities throughout the United States and Canada to ensure compliance with local road regulations. For the route across the Pacific, Hudson applied its GOLD© Standard method to select a suitable vessel and transit mode which maximized the vessel’s operational load distribution while ensuring the covers would not be damaged during transit.
By planning proactively and utilizing the PEARL© management system, Hudson was able to have a network in place to move the covers once all parties were ready. Upon the completion of their manufacture, the covers were trucked across the United States to the Pacific Northwest. There, they were transported to Canada, loaded onto a vessel, and shipped across the Pacific ready to be installed onto their custom barges.
Weather Sensitive Discharging
Hudson finds an innovative solution to discharge sensitive cargo during rain.
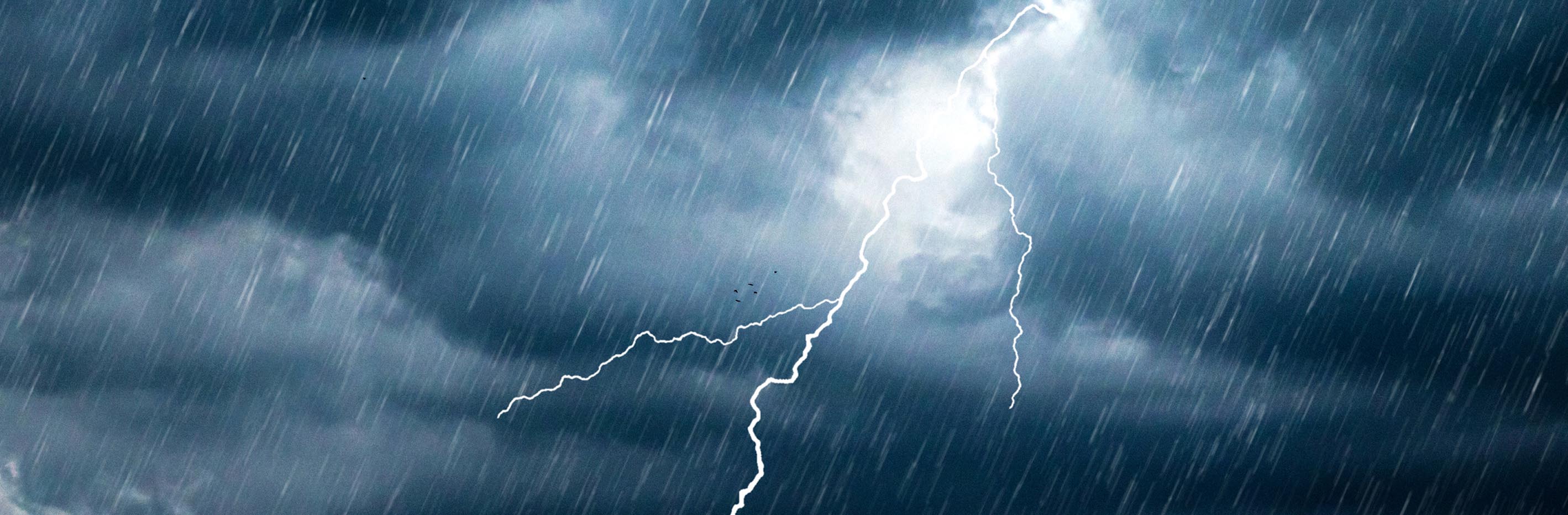
Hudson’s PEARL© management system allows seamless integration of logistics assets and personnel across continents and, as one customer discovered when they needed to unload sensitive cargo with rain approaching, enables Hudson to quickly implement creative solutions to achieve concrete results.
As Hudson brought the vessel carrying the customer’s cargo to port, Hudson's surveyors identified problematic weather patterns and began sourcing materials and personnel. The vessel’s master cracked open the hatch to be unloaded, and Hudson personnel immediately covered the opening with a thick, waterproof tarp. In order to prevent the pooling of water on the hatch, the tarp was constructed at an angle to allow water to flow harmlessly off the tarp and into the sea. Hudson’s personnel then measured and cut a precise opening in the tarp, allowing the vacuvator access to the sensitive cargo below.
By sealing the tarp around the vacuvator, the vessel was able to safely discharge during rain, reducing the vessel’s stay in port and saving time and money for another delighted Hudson customer. It is innovative solutions such as this which have earned Hudson a reputation for excellence in supply chain management, and we at Hudson look forward to applying our energy and skill to your most troublesome logistics challenges.
Linking Remote Supply Chains
Hudson integrates a remote mine in the Arctic Circle into a customer's existing supply chain.
When a client asked Hudson to seamlessly integrate a remote mine in the Arctic Circle into their supply chain, Hudson utilized its innovative PEARL© management system to streamline client operations and maximize efficiency. Instead of relying on the sparse existing infrastructure, which employed barges, ferries and trucks, Hudson constructed a shore facility capable of loading ocean going vessels to maximize the mine’s value.
The shore facility was constructed by anchoring a large barge a suitable distance from shore, then linking the barge to the mainland using a foot bridge and a conveyor. The facility was capable of handling vessels up to 40,000MT DWT and the conveyor was capable of loading up to 2,000MT per hour. By using this type of set up, Hudson was able to locate the facility 1.5 miles from the primary crusher machine while still being able to service all types of bulk carrier vessels regardless of gearing.
By eliminating road and lightering operations, Hudson maximized the mine’s flexibility and efficiency, resulting in one very satisfied customer. This innovative and effective solution is a characteristic outcome of Hudson’s PEARL© management system, which Hudson employs to overcome its customer’s most difficult supply chain challenges.